The
crafting of a Ginko porcelain piece begins with one of its
most striking features - its color. First we prepare a richly colored
clay body by mixing various proportions of stains into
a simple
porcelain recipe.
The next stage
is the construction
of nerikome “logs”. First, the clay is made into flat
strips by passing it through a pasta making machine between two
pieces of fabric.
|
|
Sunyong
passes a strip of clay through a pasta maker |
The
flattened strip emerges from the machine |
A
drawing of a design is transformed into a three
dimensional log by laminating, carving, rolling and manipulating
layers
of colored clay. These logs are then
sliced into thin cross sections.
|
|
|
A stack
of full-sized nerikome logs ready for compressing |
A full-sized
log and its compressed counterpart |
The
compressed log is sliced into thin, sushi-like cross-sections |
Looking
like
thin sushi, the slices will be inlaid into the surface of a clay slab, creating
intricate
designs. Thus the 2-D drawing has been transformed into a 3-D
log
and then to a 2-D surface design which is integrated into a 3-D piece.
Forms
are initially created by carving blocks of plaster or using
plaster
molds cast from wheel- thrown forms.
Using these
molds, master forms (such as plates, bowls etc) are made
which will be used to make the hydraulic clay press mold. |
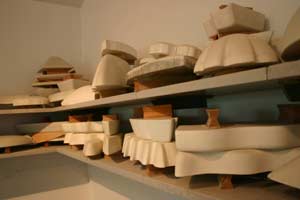 |
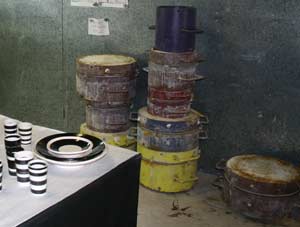 |
Making
a clay press mold for the hydraulic press is a long and strenuous
process. However utilizing this technology enables us a unique
opportunity for expanded artistic expression while keeping
the work reasonably priced
for such a labor intensive application. |
In
the first pressing we then shape the forms on the hydraulic press.
Sunyong
does all the
design work with pieces of inlays on the just pressed form. It
is then pressed a second or third time to inset the inlay.
Trimming follows, along with various finishing tasks.
Of
course, some pieces are still made entirely by hand, without
the use of the press.
After hand-finishing,
we apply a commercially available food-safe clear glaze.
Ginko Porcelain
is then single fired in a high-fire oxidation kiln, yielding
a radiant brilliance.
Grinding
the “foot” off the pottery is the final touch
and the piece is ready for use. |
|
|